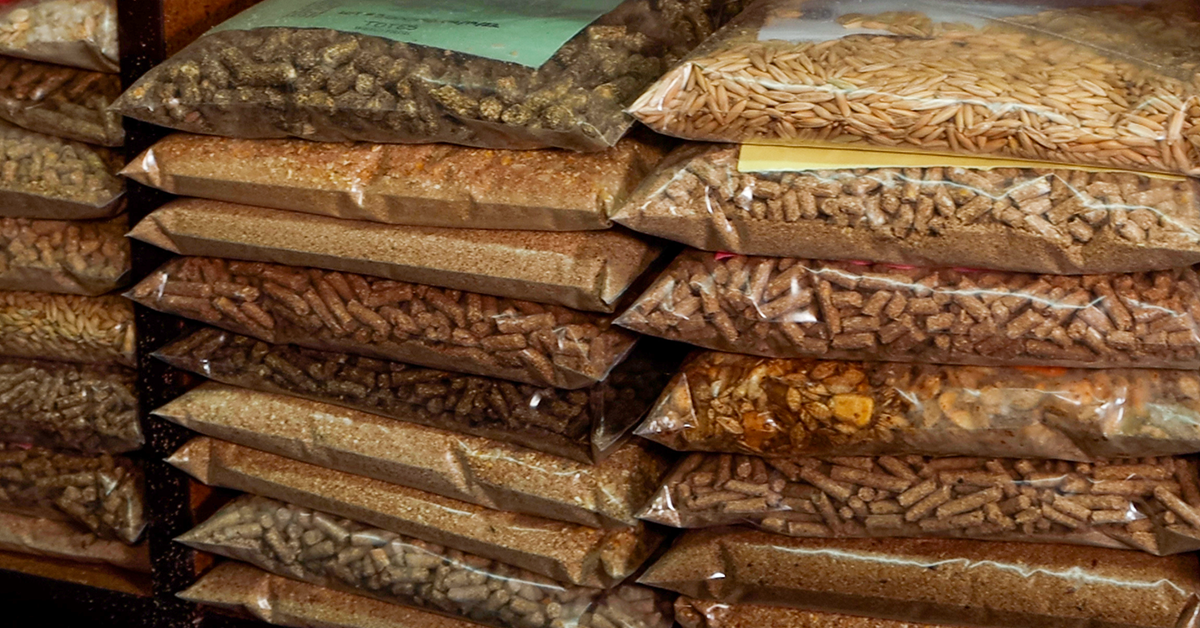
Understanding Variance in Nutrition Systems
Fact: Variability in livestock feed is a constant. At almost every point during feed production, deviation can and often will occur. In most scenarios, the degree of variability is not necessarily alarming, but it is still present. In bringing to light the areas in which deviation occurs, IFA can employ testing protocols and standards to reduce the risk of these deviations getting out of hand.
As IFA’s Quality Control/Assurance and Compliance Manager and in my supportive role as a multi-species nutritionist, I conduct forage and on-farm feed tests regularly. Raw and bagged ingredients get tested to ensure IFA feeds are made with ingredients that meet our quality standards. Finished products also get reviewed to ensure we manufacture what we list on our food labels. Additionally, our team manages various specialty, forage, and state tests. Tests range from simple crude protein checks to technical tests such as non-protein nitrogen or starch availability.
Throughout IFA’s copious and diverse testing schedule, one thing is abundantly clear: livestock feed deviations exist between what we start with or what we expect to feed and what we actually mix for our animals or what our animals actually digest. Here is a shorter version: The feed that we calculate to provide to our animals rarely matches that which we actually provide to and is utilized by our animals.
Federal and State Regulations on Livestock Feed
Before I lay out where these deviations occur within feed system processes, I do want to mention that even government agencies in charge of enforcing feed laws, both federal and state, are aware that deviations between expected (theoretical) and actual (reality) exist. For example, if we were to mix a medicated product intended as the sole ration, the FDA would allow up to 30% variance for the medication. If the expected or guaranteed level was 100 mg/lb, the FDA would allow a drug test result of 70-130 mg/lb. In Utah, a guaranteed level of 20% crude protein would still be legal with a test result of >19%; there would be no complaint from the state if the test came back at 30% because the label guarantees a minimum of 20%. For Idaho, a test result of 75 or 200 ppm for copper is passable for a label that guarantees a minimum of 100 ppm.
Why Livestock Feed Nutrients Can Vary
Let us continue with what I learned back in graduate school: “That which is in (1) feed is not that which is (2) sampled, which is not that which is (3) tested, which is not that which is (4) formulated, which is not that which is (5) manufactured, which is not that which is (6) delivered, which is not that which is (7) rationed, which is not that which is (8) consumed, which is not that which is (9) digested, which is not that which is (10) utilized.”
In short, deviation from original feed ingredients compounds the further away that feed is commingled, sampled, mixed, delivered, and ultimately consumed and utilized.
1. Growing Conditions
Consider the most common feed ingredient in all livestock nutrition: corn. In the United States, we have producers growing corn in cold and humid climates with short seasons, dry farms at sea level and higher, flood-irrigated desert fields, fields with aquifer-fed pivots, and so forth. Growing conditions are diverse enough to create variance in nutrient profiles. Growing conditions that affect downwind processes such as flaking quality. To further the point, the harvesting process also aids in the variance: moisture content, bushel weight, kernel damage, weed infestations, chaff and cobb contamination, etc.
Aside from those variances, corn is sold the same whether it comes from the mountain valley or the desert basin. Corn grown in the desert Southwest cannot be expected to test the same as corn from Cache Valley. Even more, I would not expect corn grown in Cache Valley to be nutrient twins with corn from the Wasatch Front (Sidenote: I know this because I have seen hundreds of tests confirming this). Even more, I would not expect corn from two different producers in Cache Valley to be nutrient equivalent. Even more, I would not expect corn from two different fields from the same producer to be nutrient equivalent. Even more, I would not expect corn from opposite ends of the same field from a Cache Valley producer to be nutrient equivalent.
2. Sampling Process
The task of pulling a sample can create variance. A lone sample from a 35-ton corn delivery, despite best efforts to conglomerate subsamples, provides only a convenient snapshot of the nutrient profile of that corn load. If that sample is not correctly acquired, our expectation can be downgraded. Sampling from just one location in that truck will not provide a clear representative sample of that load. Sampling from one hay bale or one side of the bunk does not represent the entirety of the stack or feed row. For on-farm samples, time of day, location of bunk, animal exposure and sorting of feed, number of bales included, or location within the silage bag may affect the accuracy of sampling.
3. Testing Labs Procedures
Interestingly, like governing agencies, testing labs are also familiar with the risk of variance and will often grind and test multiple subsamples to reduce analytical variance. However, I have witnessed duplicate tests from the same submitted sample vary greater than 1.5% in crude protein. Test results can be influenced by lab technician experience, number of subsamples tested, testing procedures utilized, and capability of analytic machines employed.
4. Formulation Software Measurement
As the corn is used by the feed mill, formulation software takes all available nutrient analytics that the user provides to it and calculates expected nutrient specs. If those analytics already contain variances from the feed through testing, or the incorporation of those analytics provided contains computational or user errors, expected nutrient guarantees further stray from the actual.
5. Multiple Ingredients in Manufacturing and Delivery
The feed mill will accumulate multiple corn deliveries from multiple sources into one storage container. This makes nutrient accuracy a moving target with corn moving out of the system while more corn enters the system. Manufacturing also adds to variance through the inherent differences between suppliers of the same product and machinery used to manufacture feed. Place of origin for minerals, place of manufacture for vitamins, type of processing for added-value ingredients, scale precision. When mixing multiple ingredients, variances across the board get compounded to feed being delivered.
6. Uniform Ration Mixing
On a farm, the same deviations may occur across forages and other bulk ingredients along with the delivered feed from the mill and mixer variations at the farm. Uniform ration mixing and delivery to livestock can be two of the greatest sources of variation in livestock nutrition. Incomplete mixing, forage length, forage maturity at harvest, discrepancies in ingredient inclusion, and delivery method and consistency all affect end-user utilization.
7. Livestock Personality and Gut Health
Add to those deviations the fact that we have bullies and picky eaters in the corral. A beautiful display of partially-or fully-mixed feed at the bunk will be ravaged by the bullies and sorted by the pickers. And the gut and overall health of those animals will also dictate how that feed is digested and utilized within the individual.
How to Decrease Livestock Feed Variances
At IFA, we employ multiple protocols and standards to reduce our risk of deviation. We have recognized grain and by-product standards at each mill. Mill processes and procedures are established. A bulk ingredient testing schedule is in place. Mill personnel are trained regularly on quality control requirements, and corrective actions are employed when deviation from the processes or standards occurs. Multiple industry quality certifications are audited and renewed yearly to further solidify our commitment to producing safe and quality feed.
There might already be procedures and standards in place at your facility that reduce your risk of deviation. Mixing protocols, spot checks on incoming ingredients, preventative maintenance schedules, personnel training, regular ingredient and TMR tests, and other processes help reduce the variance.
In conclusion, variance in any feed program will always exist in the background. It can occur at multiple points in the process, and if little is done to reduce variance at one stage, the risk of greater variance in the following stages rises. In a functional nutrition program, variance should not only be acknowledged as a reality but also be managed to limit its effect.
Find an IFA Feed & Nutrition Advisor in your area
Written by Jamie Allen, Ph.D., IFA Quality Assurance and Compliance Manager, and originally published in the IFA Cooperator magazine (vol. 89, no. 4) Winter 2023.
Jamie Allen is the Quality Assurance and Compliance Manager with IFA. Jamie also finds time to do on-farm nutrition consulting. Jamie earned his bachelor's degree from Brigham Young University Idaho and his master’s degree in animal science from the University of Idaho where he worked at the university farm and aided in several range, dairy and feedlot nutrition projects. He went on to earn his PhD in ruminant nutrition and management from the University of Arizona where he also conducted his post-doctoral research. Jamie taught four years at Northwest Missouri State University as an assistant professor of animal science before bringing his expertise to IFA where he manages all government compliance and industry certification and ensures the quality of internal feed programs.