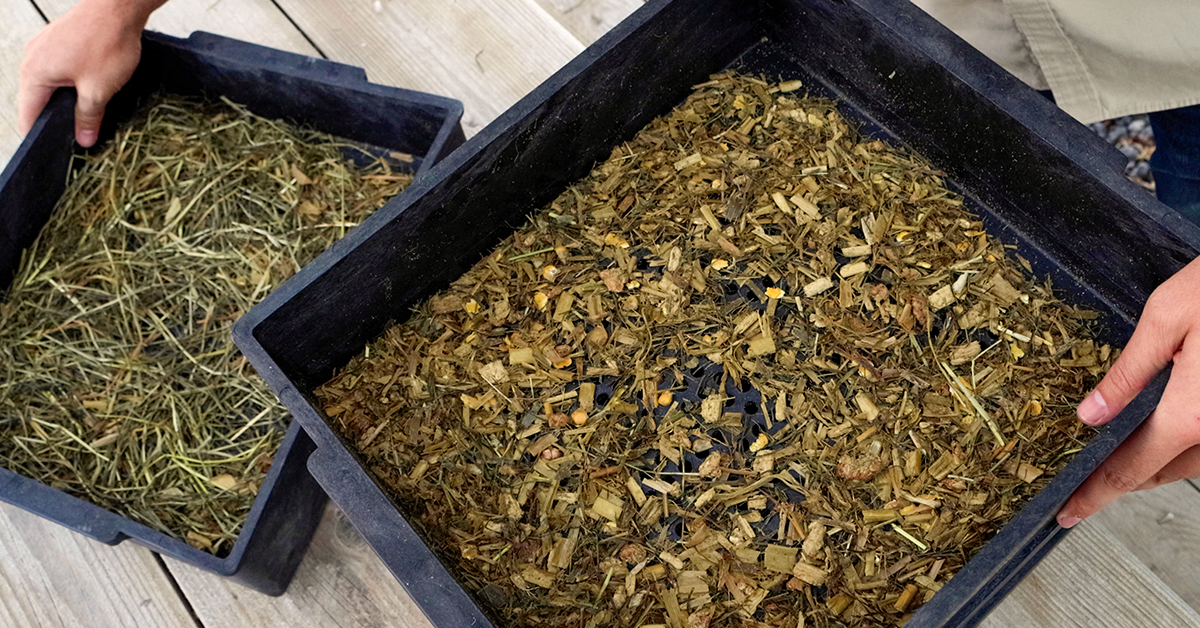
Measure. Mix. Monitor. Ensuring dairy and feedlot cows get the nutrition they need requires much attention to detail when delivering farm feed.
Let me offer a simplified comparison. I don’t pretend to be a good cook. However, I like to think I do a pretty good job in front of a grill (probably true of many men). But one thing I really seem to lack is consistency. I make a great marinade and cook the steak perfectly one time, but when I try to repeat it, I can’t because I didn’t follow a recipe. My marinades consist of “a dash of this” and “a splash of that.”
This type of inconsistent approach occasionally works when feeding our production animals but can quickly lead to issues including acidosis, digestive upset and reduced feed intake. We need to be much more methodical in our approach when mixing a Total Mixed Ration (TMR) and using a mixer wagon. Some specific steps and recipes need to be followed so that our animals perform to their maximum potential. A few notable areas of farm feed to monitor are: the dry matter ingredients, the mixer wagon, and the TMR itself.
Dry Matter
The dry matter of forage and feeds is crucial when balancing a ration. When a feed sample is sent to a lab, a dry matter and moisture measurement will appear near the label’s top of the report. These two are inverses and always add to 100%.
As can probably be deduced by the terminology, the nutrients are found in the dry matter portion and only water is in the moisture portion. A couple of percentage point changes in moisture spread across hundreds of pounds of feed added to a ration can result in a large change in dry feed (and nutrients) delivered to animals. In a dairy setting, Dry Matter Intake drives milk production. So any decrease in that intake can result in losses in production and by extension, decreased checks in the mail.
Let’s look at a simple example:
Your mix sheet calls for 3000 lbs of corn silage added to your mixer. Assuming a Dry Matter percent of 32% (68% moisture), then you can calculate that your animals will be receiving 960 lbs of dry corn silage.
Now if for some reason that moisture changes (a small pile of silage sat out overnight in a rainstorm, a wet patch in the field, ect.) to 27% dry matter/73% moisture, then you would only be adding 810 lbs of dry corn silage. That is 150 lbs less than the previous situation.
There will always be some fluctuations in moisture levels of any feed or product, but they should be monitored and rations adjusted as needed.
Mixing Wagon
After ensuring your various feed ingredients are as expected, the next place of control is your mixer wagon. A few questions to ask yourself:
Is your mixer operating correctly, without any ‘dead spots’?
These dead spots are places where feed is not being mixed thoroughly, if at all. This can be due to various reasons, but in effect, the TMR will not be consistent to each animal. A simple way of monitoring this is to use a drone and fly it over the mixer as ingredients are added and watch how the mixer responds.
Are ingredients being added in the correct order so that they are mixed well?
Generally, there are two categories of mixer wagons: horizontal and vertical. Each manufacturer will most likely have specific instructions. However, if those instructions are missing, here are some guidelines.
Vertical mixer: Start with any dry forages that might have a lot of volume. Then add any grains and concentrates and finally finish with ensiled forages and liquids.
Horizontal mixer: Start with grains, liquids and concentrates. Follow that with any ensiled forages you might have and finish with dry forages.
How long are the ingredients being mixed?
In general, 5 minutes should be adequate to thoroughly mix a TMR. Any excess mixing will only reduce particle size and lower the effective fiber delivered to the animals. One quick and easy way to monitor mixing effectiveness is to watch any feed leftover in the bunk. If the leftovers look substantially different from the delivered TMR, then the animals have sorted through the feed.
These three areas are pretty simple to monitor and can lead to some quick improvements in consistency if your operation is experiencing issues.
Monitoring A TMR: Forage Particle Separator
Ok, so the drone video looks pretty good. There don’t seem to be any dead spots when mixing and the TMR looks consistent when it gets to the bunk. We’re done, right? Well, not necessarily. As they say, you can’t manage what you don’t measure.
There is a quantitative way to measure how well a TMR is mixed and delivered to the animal; it is called a shaker box, or more specifically, a Forage Particle Separator. This consists of three sieve boxes with different screen sizes sitting on top of a solid bottom box. Using a defined shaking pattern, different-length particles will be separated into different boxes. The contents of each box are then weighed and a percentage of each box is calculated.
Starting from the top sieve (largest particles) to bottom (smallest particles), distribution would be approximately:
- Top screen: 2-8%
- Second screen: 30-40%
- Third screen: 10-20%
- Bottom Pan: 30-40%
Too much weight in the top (long stems and hay) might lead to easily sorted TMRs. Excessive weight in the bottom pan could indicate too much mix time and decreased effective fiber.
Multiple samples should be taken from along the feed bunk and compared. Large deviations would show that the mixer isn’t making a consistent TMR. Ideally, each mouthful the cows take would be exactly the same.
Ensuring your animals receive consistent and well-balanced TMRs is imperative to a successful operation. Some simple measurements and monitoring help with that endeavor. Consult your local IFA feed and nutrition specialist with any questions on how to put these steps into practice. After all, your animals are far more important than “a dash of this” and “a splash of that.”
Find an IFA Feed & Nutrition Advisor in your area
Written by Jeffrey Briscoe, IFA Technical Sales Assistant/Feed Sales Consultant, and originally published in the IFA Cooperator magazine (vol. 89, no. 3) Fall 2023. References: University of Minnesota Extension and Penn State Extension.
Jeffrey Briscoe helps intermountain producers as a Technical Sales Assistant with IFA Feed and Nutrition. Jeffery has extensive experience with livestock growing up on a small Oregon farm and helping with his grandfather’s cattle. He earned his degree in Animal, Dairy and Veterinary Science with an emphasis in Animal Production from Utah State University. Jeffery works closely with IFA’s nutritionists to provide on-farm services for producers as well as assist with quality control at IFA’s North Region Feed Mill. He enjoys getting out in the field and working with producers but can also be found enjoying the great outdoors with his wife–but don’t get confused. You might think you’ve spotted him out exploring when it could just be his twin!